Quick Inquiry
Heat exchangers are complex devices that require a careful selection of tubes to achieve optimal heat transfer efficiency. Serrated finned tubes are becoming increasingly popular in various industries due to their unique design and ability to improve heat exchange processes. This article provides an in-depth look at these tubes, exploring their manufacturing process, features, and the advantages they offer to businesses operating finned tubes.
What Are Serrated Finned Tubes?
Serrated finned tubes stand out as a specialised category of heat exchanger tubes crafted to enhance the efficiency of heat transfer processes. What sets them apart is the incorporation of serrations – small notches or grooves along the fins. These serrations are strategically designed to disrupt the air or gas flow boundary layer over the finned surface, leading to improved heat transfer characteristics.
The primary objective of these serrations is to create turbulence in the airflow, preventing the formation of a stagnant boundary layer that could impede the heat exchange process. This unique design significantly differentiates serrated finned tubes from their traditional counterparts, making them particularly suitable for applications where heightened heat transfer efficiency is crucial.
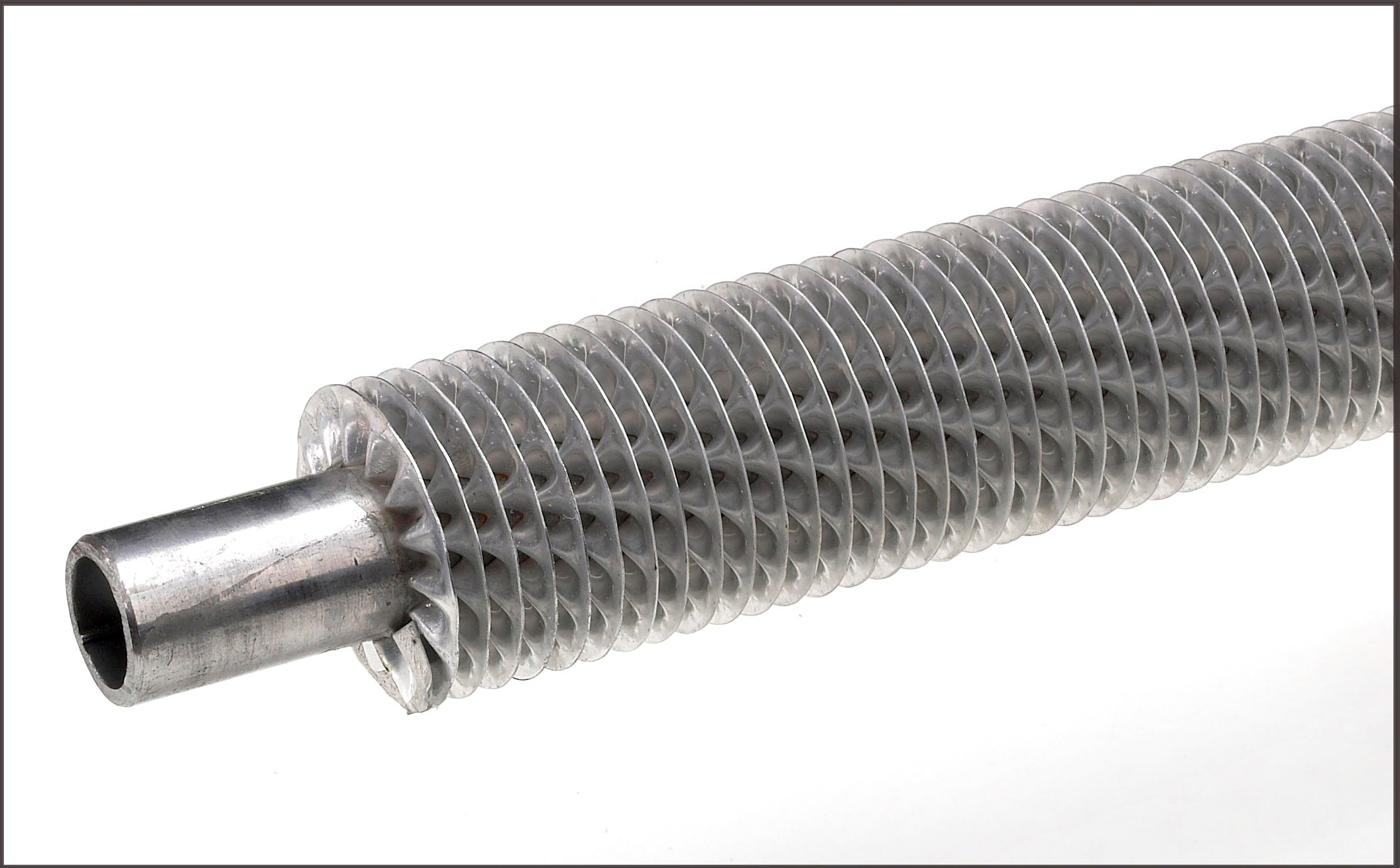
How Are Serrated Finned Tubes Manufactured?
The manufacturing process of serrated finned tubes involves specialised steps, ensuring precision and quality for optimal performance. A brief overview of the critical manufacturing stages provides insight into the complexity of producing these innovative tubes:
1. Tube Production:
The journey begins with the production of the base tube, often composed of materials like alloy steel. For precision and uniformity, seamless tubes, especially those cold-drawn, are frequently preferred. This initial step sets the foundation for a tube that can withstand the rigours of diverse industrial applications.
2. Fin Formation:
The fins are then meticulously attached to the tube surface using advanced techniques. The process involves machining or extruding the serrations onto the fins, a critical step that demands precision to ensure the effectiveness of the serrations in disrupting the boundary layer. The intricacy of this process emphasises the importance of precision engineering in achieving optimal heat transfer efficiency.
3. Quality Control:
Stringent quality control measures are implemented throughout the manufacturing process to guarantee the structural integrity and performance of the finned tubes. Non-destructive testing methods, such as ultrasonic testing and visual inspections, are commonly employed to identify and rectify any defects that may compromise the functionality of the tubes.
4. Surface Coating (Optional):
In certain applications, a surface coating may be applied to the serrated finned tubes to enhance corrosion resistance and overall durability. This optional step ensures the tubes can withstand harsh operating environments, extending their lifespan.
Features of Serrated Finned Tubes
1. Enhanced Heat Transfer:
The distinctive serrations on the fins are pivotal in disrupting the airflow boundary layer. This disruption leads to increased turbulence, subsequently improving heat transfer efficiency. Serrated finned tubes excel in applications where optimising heat exchange is paramount, making them an invaluable asset across various industries.
2. Versatility:
One of the standout features of these finned tubes is their adaptability to meet specific application requirements. Available in various materials, sizes, and configurations, these tubes offer businesses the flexibility to choose the right combination for their unique heat exchanger needs. This versatility ensures a customised solution that aligns with the diverse demands of different industries.
3. Resistance to Fouling:
The design of the tubes minimises the risk of fouling by preventing the accumulation of debris on the finned surfaces. This characteristic is particularly advantageous in industries where fouling can impede heat transfer efficiency. The resistance to fouling ensures consistent performance and reduces the frequency of maintenance interventions, contributing to overall operational efficiency.
4. Durable Construction:
Manufactured from high-quality materials and subjected to rigorous quality control, serrated finned tubes boast a robust construction that ensures long-term durability and reliability. This durability is critical for industries that rely on consistent performance over extended periods, reducing downtime and maintenance costs.
5. Optimal Surface Area:
The serrated configuration not only disrupts the boundary layer but also increases the overall surface area of the finned tubes. This expanded surface area provides more opportunities for heat transfer, further enhancing the efficiency of the heat exchange process. The optimisation of the surface area is a crucial factor in achieving maximum thermal performance.
6. Uniform Heat Distribution:
Serrated finned tubes facilitate a more uniform heat distribution across the entire surface. The disruption caused by serrations prevents localised heating or cooling, ensuring that heat is evenly distributed. This uniformity is particularly beneficial in applications where precise temperature control is essential.
7. Corrosion Resistance:
The optional surface coating, when applied, enhances the corrosion resistance of the finned tubes. This feature is invaluable in environments with corrosive elements, ensuring the tubes maintain their structural integrity and performance even in challenging conditions.
Read here about how to protect tubes and pipes from corrosion.
Advantages of Serrated Finned Tubes
Understanding the advantages of serrated finned tubes is crucial for businesses seeking optimal heat exchanger solutions. Delving deeper into the benefits these tubes offer:
1. Improved Thermal Performance:
At the forefront of advantages lies the significantly improved thermal performance achieved with the tubes. Disrupting the boundary layer and the optimised surface area enhances heat transfer efficiency. Industries relying on precise temperature control and maximum thermal performance find these tubes indispensable.
2. Energy Efficiency:
The enhanced heat transfer efficiency translates directly into improved energy efficiency. These finned tubes enable industries to achieve the desired temperature control with reduced energy consumption, leading to tangible cost savings and environmental benefits. This advantage aligns with the global push towards sustainable and energy-efficient practices.
3. Extended Equipment Lifespan:
The resistance to fouling and durable construction of serrated finned tubes contribute to an extended lifespan of heat exchanger equipment. The prevention of fouling reduces the frequency of maintenance interventions, minimising downtime. The extended equipment lifespan translates into long-term cost savings and reliability for industries relying on continuous and efficient heat exchange processes.
4. Customization Options:
Serrated finned tubes offer unparalleled versatility in design, allowing businesses to tailor the heat exchanger system to their specific needs. The ability to customise materials, sizes, and configurations ensures that the tubes meet the unique requirements of various industries and applications. This adaptability positions the tubes as a versatile solution for a diverse range of thermal management challenges.
5. Cost-Effective Solution:
Combining improved thermal performance, energy efficiency, and extended equipment lifespan makes serrated finned tubes a cost-effective solution in the long run. While the initial investment may be higher than conventional tubes, the overall operational savings, reduced maintenance costs, and extended lifespan make them a wise investment for industries looking to optimise their heat exchange processes.
Specific Applications of Serrated Finned Tubes
With their innovative design and enhanced heat transfer capabilities, serrated finned tubes find diverse applications across industries that rely on efficient thermal management. Here are vital points outlining specific applications where these tubes prove invaluable:
Oil and Gas Industry:
- These finned tubes excel in heat exchangers used for oil refining and processing.
- Their resistance to fouling makes them ideal for applications where maintaining consistent heat transfer efficiency is critical.
Power Generation Plants:
- The tubes are crucial in power plants, mainly boilers and condensers.
- The increased surface area and optimal heat distribution improve thermal performance in power generation processes.
Chemical Processing Facilities:
- Industries involved in chemical manufacturing leverage these tubes in heat exchangers for precise temperature control.
- The corrosion-resistant properties ensure durability in chemically aggressive environments.
HVAC Systems:
- Heating, Ventilation, and Air Conditioning (HVAC) systems benefit from the energy efficiency of serrated finned tubes.
- Their ability to distribute heat uniformly is essential for maintaining comfortable indoor environments.
Automotive Radiators:
- These tubes are increasingly used in automotive radiators for efficient heat dissipation.
- The enhanced thermal performance contributes to improved engine efficiency and reduced fuel consumption.
Aerospace Heat Exchangers:
- Aerospace applications, including aircraft and spacecraft, rely on these finned tubes for lightweight and efficient heat exchange solutions.
- The tubes’ durability and ability to withstand extreme conditions make them suitable for aerospace environments.
Food and Beverage Processing:
- These tubes play a key role in maintaining precise temperatures during various stages of food and beverage processing.
- The tubes’ resistance to fouling is advantageous in ensuring compliance with hygiene standards.
Petrochemical Industry:
- In petrochemical plants, where stringent temperature control is essential, these finned tubes are employed in heat exchangers.
- Their versatility allows customisation to meet specific requirements in diverse petrochemical processes.
We Manufacture A Variety of Seamless Tubes and Finned Tubes
Discover unparalleled quality and innovation with our extensive range of seamless tubes and fin tubes tailored to your diverse industrial needs. At Anand Seamless Ltd, we take pride in manufacturing a variety of finned tubes, including serrated finned tubes, pin tubes, spiral fin tubes, extruded fin tubes, and more.
Our commitment to precision engineering, cutting-edge technology, and stringent quality control ensures that each tube leaving our facility exceeds industry standards. Whether you operate in oil and gas, power generation, chemical processing, HVAC, or any other industry requiring superior thermal management, our tubes, and pipes are designed to optimise heat transfer efficiency.
Experience the difference between unmatched durability, energy efficiency, and customised solutions. Partner with us for seamless tubes that set new benchmarks in performance. Contact us at +91-9099996851 or write to us at inquiry@anandseamless.com to explore our comprehensive range of fin tubes tailored for your business.
lATEST BLOG |
The Rise of Finned Copper Tubes in High-Performance Cooling Systems
In today’s fast-paced world of industrial in |
Role of Finned Tubes in Waste Heat Recovery Systems
In today’s industrial world, where energy effici |
Why Cold-Drawn Tubes Are Ideal for High-Pressure Applications
In industries where materials are pushed to the ed |
Common Seamless Tube Defects and How Manufacturers Prevent Them
Seamless tubes are the backbone of many critical a |
10 Questions to Ask Your Seamless Pipe Manufacturer Before Ordering
When sourcing steel seamless pipes, choosing the r |